Kompozyt z osnową ceramiczną - Ceramic matrix composite

Kompozyty z osnową ceramiczną ( CMC ) stanowią podgrupę materiałów kompozytowych i podgrupę ceramiki . Składają się z włókien ceramicznych osadzonych w ceramicznej osnowie. Zarówno włókna, jak i matryca mogą składać się z dowolnego materiału ceramicznego, przy czym włókna węglowe i węglowe można również uważać za materiał ceramiczny.
Wstęp
Motywacja opracowanie CMC było przezwyciężenie problemów związanych z konwencjonalnymi ceramiki technicznych, takich jak tlenek glinu , z węglika krzemu , azotku glinu , azotku krzemu lub ditlenku cyrkonu - to złamanie łatwo w warunkach mechanicznego i termicznego obciążenia mechanicznego z powodu pęknięć zapoczątkowanych małych wad lub rys. Odporność na pękanie jest bardzo niska, jak w przypadku szkła. W celu zwiększenia odporności na pękanie lub odporności na pękanie , w osnowę wbudowano cząstki (tzw. monokrystaliczne wiskery lub płytki ). Jednak poprawa była ograniczona, a produkty znalazły zastosowanie tylko w niektórych ceramicznych narzędziach skrawających. Jak dotąd tylko integracja długich włókien wielożyłowych drastycznie zwiększyła odporność na pękanie, wydłużenie i odporność na szok termiczny i zaowocowała kilkoma nowymi zastosowaniami. Wzmocnienia stosowane w kompozytach z osnową ceramiczną (CMC) służą do zwiększenia odporności na pękanie połączonego systemu materiałów, przy jednoczesnym wykorzystaniu naturalnej wysokiej wytrzymałości i modułu Younga osnowy ceramicznej. Najpopularniejszym przykładem wykonania wzmocnienia jest włókno ceramiczne o ciągłej długości, o module sprężystości, który jest zazwyczaj nieco niższy niż osnowy. Funkcjonalna rola tego włókna polega na (1) zwiększeniu naprężenia CMC dla postępu mikropęknięć w osnowie, zwiększając w ten sposób energię zużywaną podczas propagacji pęknięć; a następnie (2), gdy pęknięcia na całej grubości zaczynają tworzyć się na CMC przy wyższym naprężeniu (proporcjonalne naprężenie graniczne, PLS), aby zniwelować te pęknięcia bez pękania, zapewniając w ten sposób CMC wysoką wytrzymałość na rozciąganie (UTS). W ten sposób wzmocnienia z włókien ceramicznych nie tylko zwiększają początkową odporność struktury kompozytu na propagację pęknięć, ale także pozwalają CMC uniknąć nagłego kruchego pękania, charakterystycznego dla ceramiki monolitycznej. To zachowanie różni się od zachowania włókien ceramicznych w kompozytach z osnową polimerową (PMC) i kompozytach z osnową metaliczną (MMC), gdzie włókna zazwyczaj pękają przed osnową ze względu na większe możliwości odkształcenia niszczącego tych osnowy.
Węgiel (C), specjalny węglik krzemu (SiC), tlenek glinu ( Al
2O
3) i mulit ( Al
2O
3−SiO
2) włókna są najczęściej stosowane do CMC. Materiały osnowy są zwykle takie same, to znaczy C, SiC, tlenek glinu i mulit. W niektórych układach ceramicznych, w tym SiC i azotku krzemu, procesy nieprawidłowego wzrostu ziarna mogą skutkować mikrostrukturą wykazującą wydłużone duże ziarna w matrycy o drobniejszych zaokrąglonych ziarnach. Mikrostruktury pochodzące z AGG wykazują hartowanie ze względu na mostkowanie pęknięć i ugięcie pęknięć przez wydłużone ziarna, co można uznać za wzmocnienie z włókien wytwarzanych na miejscu. Ostatnio ceramika ultrawysokotemperaturowa (UHTC) była badana jako osnowa ceramiczna w nowej klasie CMC, tak zwanych kompozytach z osnową ceramiczną o ultrawysokiej temperaturze (UHTCMC) lub kompozytami ceramicznymi o ultrawysokiej temperaturze (UHTCC).
Ogólnie nazwy CMC zawierają kombinację typu włókna/rodzaju matrycy . Na przykład C/C oznacza węgiel wzmocniony włóknem węglowym ( węgiel/węgiel ), a C/SiC oznacza węglik krzemu wzmocniony włóknem węglowym. Czasami proces produkcyjny jest uwzględniony, a kompozyt C/SiC wytwarzany w procesie infiltracji ciekłego polimeru (LPI) (patrz poniżej) jest skracany jako LPI-C/SiC .
Ważnymi komercyjnie dostępnymi CMC są C/C, C/SiC, SiC/SiC i Al
2O
3/Glin
2O
3. Od ceramiki konwencjonalnej różnią się następującymi właściwościami, szczegółowo przedstawionymi poniżej:
- Wydłużenie do zerwania do 1%
- Silnie zwiększona odporność na pękanie
- Ekstremalna odporność na szok termiczny
- Ulepszona zdolność dynamicznego obciążenia
- Właściwości anizotropowe zależne od orientacji włókien
Produkcja
Procesy produkcyjne zwykle składają się z następujących trzech etapów:
- Układanie i mocowanie włókien w kształcie pożądanego komponentu
- Infiltracja materiału matrycy
- Obróbka końcowa i w razie potrzeby dalsze zabiegi, takie jak powlekanie lub impregnacja wewnętrznej porowatości .
Pierwszy i ostatni krok są prawie takie same dla wszystkich CMC: W kroku pierwszym włókna, często nazywane niedoprzędami, są układane i mocowane za pomocą technik stosowanych w tworzywach sztucznych wzmocnionych włóknami, takich jak układanie tkanin , nawijanie włókien, splatanie i wiązanie . Wynik tej procedury nazywa się preformą włóknistą lub po prostu preformą .
W drugim etapie stosuje się pięć różnych procedur do wypełnienia matrycy ceramicznej pomiędzy włóknami preformy:
- Osadzanie z mieszaniny gazów
- Piroliza polimeru preceramicznego
- Reakcja chemiczna pierwiastków
- Spiekanie w stosunkowo niskiej temperaturze w zakresie 1000–1200 °C (1830–2190 °F)
- Osadzanie elektroforetyczne proszku ceramicznego
Procedury pierwsza, druga i trzecia znajdują zastosowanie w przypadku nietlenkowych CMC, podczas gdy czwarta jest stosowana dla tlenkowych CMC; praktykowane są również kombinacje tych procedur. Piąta procedura nie została jeszcze ustalona w procesach przemysłowych. Wszystkie procedury mają podwarianty, które różnią się szczegółami technicznymi. Wszystkie procedury dają porowaty materiał.
Trzeci i ostatni etap obróbki – szlifowanie , wiercenie , docieranie lub frezowanie – musi być wykonany za pomocą narzędzi diamentowych. CMC można również poddawać obróbce strumieniem wody , laserem lub ultradźwiękami .
Włókna ceramiczne
Włókna ceramiczne w CMC mogą mieć strukturę polikrystaliczną , tak jak w tradycyjnej ceramice. Mogą być również amorficzne lub mieć niejednorodny skład chemiczny , który powstaje w wyniku pirolizy prekursorów organicznych . Wysokie temperatury procesu wymagane do produkcji CMC wykluczają stosowanie włókien organicznych, metalowych lub szklanych . Można stosować tylko włókna stabilne w temperaturach powyżej 1000 °C (1800 °F), takie jak włókna z tlenku glinu, mulitu, SiC, tlenku cyrkonu lub węgla. Włókna amorficzne SiC mają zdolność wydłużenia powyżej 2% – znacznie większą niż w konwencjonalnych materiałach ceramicznych (0,05 do 0,10%). Powodem tej właściwości włókien SiC jest to, że większość z nich zawiera dodatkowe pierwiastki, takie jak tlen , tytan i/lub aluminium, dające wytrzymałość na rozciąganie powyżej 3 GPa. Te ulepszone właściwości sprężyste są wymagane w przypadku różnych trójwymiarowych układów włókien (patrz przykład na rysunku) w produkcji tekstyliów , gdzie niezbędny jest mały promień gięcia.
Procedury produkcyjne
Osadzanie matrycy z fazy gazowej
Do tego celu dobrze nadaje się chemiczne osadzanie z fazy gazowej (CVD). W obecności preformy włókien CVD zachodzi pomiędzy włóknami i ich pojedynczymi włóknami i dlatego nazywa się to infiltracją z fazy gazowej (CVI). Jednym z przykładów jest produkcja kompozytów C/C: preforma z włókna C jest poddawana działaniu mieszaniny argonu i gazu węglowodorowego ( metanu , propanu itp.) pod ciśnieniem około 100 kPa lub niższym i w temperaturze powyżej 1000 ° C. Gaz rozkłada się osadzając węgiel na i pomiędzy włóknami. Innym przykładem jest osadzanie węglika krzemu, które zwykle prowadzi się z mieszaniny wodoru i metylotrichlorosilanu (MTS, CH
3SiCl
3; jest również powszechny w produkcji silikonu ). W określonych warunkach ta mieszanina gazów osadza drobny i krystaliczny węglik krzemu na gorącej powierzchni w preformie.
Ta procedura CVI pozostawia ciało o porowatości około 10-15%, ponieważ dostęp reagentów do wnętrza preformy jest coraz bardziej blokowany przez osadzanie się na zewnątrz.
Tworzenie matrycy poprzez pirolizę polimerów zawierających C i Si
Polimery węglowodorów kurczą się podczas pirolizy , a po odgazowaniu tworzą węgiel o bezpostaciowej strukturze podobnej do szkła, który poprzez dodatkową obróbkę cieplną może zmienić się w strukturę bardziej podobną do grafitu . Inne specjalne polimery znane jako polimery preceramic którym niektóre atomy węgla są zastąpione atomami krzemu, tak zwane polycarbo silany , otrzymując bezpostaciową węglik krzemu mniej więcej stechiometrycznej kompozycji. Duża różnorodność takich węglika krzemu , tlenowęgliku krzemu , węgloazotku krzemu i tlenoazotku krzemu prekursorów istnieje więcej preceramic polimery do wytwarzania polimerów pochodzące ceramiki są rozwinięte. Aby wyprodukować materiał CMC, preformę z włókien infiltruje się wybranym polimerem. Późniejsze utwardzanie i piroliza dają wysoce porowatą matrycę, co jest niepożądane w większości zastosowań. Dalsze cykle infiltracji polimeru i pirolizy są prowadzone aż do uzyskania końcowej i pożądanej jakości. Zwykle potrzeba od pięciu do ośmiu cykli.
Proces ten nazywa się infiltracją ciekłego polimeru (LPI) lub infiltracją i pirolizą polimeru (PIP). Tutaj również powszechna jest porowatość około 15% z powodu kurczenia się polimeru. Po każdym cyklu zmniejsza się porowatość.
Formowanie matrycy w wyniku reakcji chemicznej
W tej metodzie jeden materiał znajdujący się pomiędzy włóknami reaguje z drugim materiałem tworząc osnowę ceramiczną. Niektóre konwencjonalne ceramiki są również wytwarzane w reakcjach chemicznych . Na przykład azotek krzemu związany reakcją (RBSN) jest wytwarzany w reakcji proszku krzemu z azotem, a węgiel porowaty reaguje z krzemem, tworząc węglik krzemu związany reakcją, węglik krzemu, który zawiera wtrącenia fazy krzemowej. Przykładem produkcji CMC, który został wprowadzony do produkcji ceramicznych tarcz hamulcowych , jest reakcja krzemu z porowatą preformą C/C. Temperatura procesu wynosi powyżej 1414 °C (2577 °F), czyli powyżej temperatury topnienia krzemu, a warunki procesu są kontrolowane tak, że włókna węglowe preformy C/C prawie całkowicie zachowują swoje właściwości mechaniczne. Proces ten nazywa się infiltracją ciekłego krzemu (LSI). Czasami i ze względu na swój punkt wyjścia z C/C, materiał jest skracany jako C/C-SiC . Materiał wytworzony w tym procesie ma bardzo niską porowatość około 3%.
Formowanie matrycy przez spiekanie
Proces ten jest wykorzystywany do wytwarzania materiałów CMC z włókien tlenkowych/matrycy tlenkowej. Ponieważ większość włókien ceramicznych nie może wytrzymać normalnych temperatur spiekania powyżej 1600 °C (2910 °F), do infiltracji preformy włókien tlenkowych stosuje się specjalne płyny prekursorowe . Prekursory te umożliwiają spiekanie, czyli procesy formowania ceramiki w temperaturach 1000–1200°C. Są to, na przykład na bazie mieszaniny tlenku glinu, proszku cieczy tetra-etylo-orto krzemian (Si jako dawcy) i glin butanolanu potasu (jako Al dawcy), które dają się mulit matrycy. Stosowane są również inne techniki, takie jak chemia procesowa zol-żel . CMC otrzymane tym sposobem mają zwykle wysoką porowatość około 20%.
Matryca utworzona przez elektroforezę
W procesie elektroforetycznym naładowane elektrycznie cząstki rozproszone w specjalnej cieczy są transportowane przez pole elektryczne do preformy, która ma przeciwną biegunowość ładunku elektrycznego. Proces ten jest w fazie rozwoju i nie jest jeszcze wykorzystywany przemysłowo. Również tutaj należy się spodziewać pewnej pozostałej porowatości.
Nieruchomości
Właściwości mechaniczne
Podstawowy mechanizm właściwości mechanicznych
Wspomniana wysoka odporność na pękanie lub pękanie wynika z następującego mechanizmu: pod obciążeniem osnowa ceramiczna pęka, jak każdy materiał ceramiczny, przy wydłużeniu około 0,05%. W CMC osadzone włókna wypełniają te pęknięcia (patrz rysunek). Mechanizm ten działa tylko wtedy, gdy matryca może ślizgać się wzdłuż włókien, co oznacza, że musi istnieć słabe wiązanie między włóknami a matrycą. Silne wiązanie wymagałoby bardzo dużej zdolności do wydłużania włókna mostkującego pęknięcie i powodowałoby pękanie kruche, jak w przypadku konwencjonalnej ceramiki. Produkcja materiału CMC o wysokiej odporności na pękanie wymaga etapu osłabienia tego wiązania między włóknami a osnową. Osiąga się to poprzez osadzanie cienkiej warstwy węgla pirolitycznego lub azotku boru na włóknach, co osłabia wiązanie na granicy włókno/matryca, prowadząc do wyciągania włókien na powierzchniach pęknięć, jak pokazano na zdjęciu SEM u góry Ten artykuł. W tlenkowych CMC wysoka porowatość matrycy wystarcza do ustanowienia słabego wiązania.
Własności przy obciążeniach rozciągających i zginających, odporność na pękanie
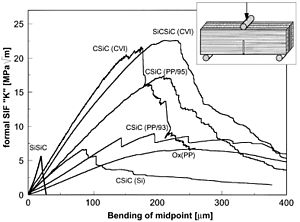
Legenda: SiSiC: konwencjonalne SiSiC , SiCSiC(CVI) i CSiC(CVI): SiC/SiC i C/SiC wytwarzane w procesach CVI, CSiC(95) i CSiC(93): C /SiC wytwarzany metodą LPI, Ox(PP): tlenkowy kompozyt ceramiczny, CSiC(Si): C/SiC wytwarzany w procesie LSI.
Wpływ i jakość interfejsu światłowodu można ocenić na podstawie właściwości mechanicznych. Pomiary odporności na pękanie wykonano na próbkach z karbem (patrz rysunek) w tzw. testach SENB (single edge-notch-bend). W mechanice pękania zmierzone dane (siła, geometria i powierzchnia pęknięcia) są normalizowane w celu uzyskania tak zwanego współczynnika intensywności naprężeń (SIF), K Ic . Ze względu na złożoną powierzchnię pęknięć (patrz rysunek na początku tego artykułu) nie można określić rzeczywistej powierzchni pęknięć dla materiałów CMC. Pomiary zatem wykorzystują początkowy karb jako powierzchnię pęknięcia, dając formalny SIF pokazany na rysunku. Wymaga to identycznej geometrii do porównywania różnych próbek. Obszar pod tymi krzywymi daje zatem względne wskazanie energii wymaganej do przemieszczenia końcówki pęknięcia przez próbkę (siła razy długość drogi daje energię). Maksima wskazują poziom obciążenia niezbędny do propagacji pęknięcia przez próbkę. W porównaniu z próbką konwencjonalnej ceramiki SiSiC można poczynić dwie obserwacje:
- Wszystkie testowane materiały CMC potrzebują o kilka rzędów wielkości więcej energii, aby rozprzestrzenić pęknięcie w materiale.
- Siła wymagana do propagacji pęknięć różni się w zależności od typu CMC.
Rodzaj materiału |
Glin 2O 3/Glin 2O 3 |
Glin 2O 3 |
CVI-C/SiC | LPI-C/SiC | LSI-C/SiC | SiSiC |
---|---|---|---|---|---|---|
Porowatość (%) | 35 | <1 | 12 | 12 | 3 | <1 |
Gęstość (g/cm 3 ) | 2,1 | 3,9 | 2,1 | 1,9 | 1,9 | 3.1 |
Wytrzymałość na rozciąganie (MPa) | 65 | 250 | 310 | 250 | 190 | 200 |
Wydłużenie (%) | 0,12 | 0,1 | 0,75 | 0,5 | 0,35 | 0,05 |
Moduł Younga (GPa) | 50 | 400 | 95 | 65 | 60 | 395 |
Wytrzymałość na zginanie (MPa) | 80 | 450 | 475 | 500 | 300 | 400 |
W tabeli CVI, LPI i LSI oznaczają proces produkcji materiału C/SiC. Dane dotyczące tlenkowych CMC i SiSiC pochodzą z arkuszy danych producentów. Wytrzymałość na rozciąganie SiSiC i Al
2O
3zostały obliczone na podstawie pomiarów wydłużenia do zerwania i modułu Younga , ponieważ ogólnie dostępne są tylko dane dotyczące wytrzymałości na zginanie tych materiałów ceramicznych. W tabeli podane są wartości uśrednione i możliwe są znaczne różnice, nawet w ramach jednej trasy produkcyjnej.
Próby rozciągania CMC zwykle pokazują nieliniowe krzywe naprężenie-odkształcenie, które wyglądają tak, jakby materiał odkształcał się plastycznie. Nazywa się to quasi- plastycznym , ponieważ efekt jest powodowany przez mikropęknięcia, które tworzą się i mostkują wraz ze wzrostem obciążenia. Ponieważ moduł Younga włókien przenoszących obciążenie jest generalnie niższy niż modułu osnowy, nachylenie krzywej zmniejsza się wraz ze wzrostem obciążenia.
Krzywe z testów zginania wyglądają podobnie do tych z pomiarów odporności na pękanie pokazanych powyżej.
Następujące cechy są niezbędne do oceny danych dotyczących zginania i rozciągania CMC:
- Materiały CMC o niskiej zawartości osnowy (do zera) mają wysoką wytrzymałość na rozciąganie (zbliżoną wytrzymałością na rozciąganie włókna), ale niską wytrzymałość na zginanie .
- Materiały CMC o niskiej zawartości włókien (do zera) mają wysoką wytrzymałość na zginanie (zbliżoną wytrzymałością ceramiki monolitycznej), ale nie mają wydłużenia powyżej 0,05% pod obciążeniem rozciągającym.
Podstawowym kryterium jakości CMC jest odporność na pękanie lub odporność na pękanie.
Inne właściwości mechaniczne
W wielu elementach CMC włókna są ułożone jako dwuwymiarowe (2D) ułożone w stos tkaniny o splocie gładkim lub satynowym . Tak więc otrzymany materiał jest anizotropowy , a dokładniej ortotropowy . Pęknięcie między warstwami nie jest mostkowane włóknami. Dlatego międzywarstwowa wytrzymałość na ścinanie (ILS) i wytrzymałość prostopadła do orientacji włókien 2D są dla tych materiałów niskie. Delaminacja może wystąpić łatwo pod pewnymi obciążeniami mechanicznymi. Trójwymiarowe struktury włókien mogą poprawić tę sytuację (patrz mikrograf powyżej).
Materiał | CVI-C/SiC | LPI-C/SiC | LSI-C/SiC | CVI-SiC/SiC |
---|---|---|---|---|
Wytrzymałość na ścinanie międzywarstwowe (MPa) | 45 | 30 | 33 | 50 |
Wytrzymałość na rozciąganie w pionie do płaszczyzny tkaniny (MPa) | 6 | 4 | – | 7 |
Wytrzymałość na ściskanie w pionie do płaszczyzny tkaniny (MPa) | 500 | 450 | – | 500 |
Na wytrzymałość na ściskanie podane w tabeli są niższe niż w przypadku konwencjonalnych materiałów ceramicznych, gdzie wartości powyżej 2000 MPa wspólnych; jest to wynikiem porowatości.
Kompozytowa struktura pozwala na duże obciążenia dynamiczne. W tak zwanym niskim cyklu zmęczenia (LCF) lub wysokiego stopnia zmęczenia (HCF) testuje Materiał doświadcza obciążenia cykliczne pod rozciąganie i na ściskanie (LCF) lub tylko na rozciąganie (HCF) załadunku. Im wyższe naprężenie początkowe, tym krótsza żywotność i mniejsza liczba cykli do zerwania. Przy początkowym obciążeniu 80% wytrzymałości próbka SiC/SiC przetrwała około 8 milionów cykli (patrz rysunek).
Współczynnik Poissona wykazuje anomalię przy pomiarze prostopadle do płaszczyzny tkaniny, ponieważ pęknięcia międzywarstwowe zwiększają grubość próbki.
Właściwości termiczne i elektryczne
Właściwości termiczne i elektryczne kompozytu wynikają z jego składników, czyli włókien, osnowy i porów oraz ich składu. Orientacja włókien daje dane anizotropowe. CMC tlenkowe są bardzo dobrymi izolatorami elektrycznymi , a ze względu na dużą porowatość ich izolacja termiczna jest znacznie lepsza niż w przypadku konwencjonalnej ceramiki tlenkowej.
Zastosowanie włókien węglowych zwiększa przewodność elektryczną pod warunkiem, że włókna stykają się ze sobą i źródłem napięcia. Matryca z węglika krzemu jest dobrym przewodnikiem ciepła. Elektrycznie jest półprzewodnikiem , dlatego jego rezystancja maleje wraz ze wzrostem temperatury. W porównaniu z (poli)krystalicznym SiC, amorficzne włókna SiC są stosunkowo słabymi przewodnikami ciepła i elektryczności.
Materiał | CVI-C/SiC | LPI-C/SiC | LSI-C/SiC | CVI-SiC/SiC | SiSiC |
---|---|---|---|---|---|
Przewodność cieplna (p) [W/(m·K)] | 15 | 11 | 21 | 18 | >100 |
Przewodność cieplna (v) [W/(m·K)] | 7 | 5 | 15 | 10 | >100 |
Rozszerzalność liniowa (p) [10 −6 ·1/K] | 1,3 | 1.2 | 0 | 2,3 | 4 |
Rozszerzenie liniowe (v) [10 −6 ·1/K] | 3 | 4 | 3 | 3 | 4 |
Rezystywność elektryczna (p) [Ω·cm] | – | – | – | – | 50 |
Rezystywność elektryczna (v) [Ω·cm] | 0,4 | – | – | 5 | 50 |
Komentarze do tabeli: (p) i (v) odnoszą się odpowiednio do danych równoległych i pionowych do orientacji włókien w strukturze 2D włókna. Materiał LSI ma najwyższą przewodność cieplną ze względu na niską porowatość – zaletę przy stosowaniu na tarcze hamulcowe. Dane te ulegają rozproszeniu w zależności od szczegółów procesów produkcyjnych.
Konwencjonalna ceramika jest bardzo wrażliwa na naprężenia termiczne ze względu na wysoki moduł Younga i niską zdolność wydłużenia. Różnice temperatur i niska przewodność cieplna powodują lokalnie różne wydłużenia, które wraz z wysokim modułem Younga generują duże naprężenia. Powoduje to pęknięcia, rozerwanie i kruchą awarię. W CMC włókna wypełniają pęknięcia, a komponenty nie wykazują makroskopowych uszkodzeń, nawet jeśli osnowa pękła lokalnie. Zastosowanie CMC w tarczach hamulcowych pokazuje skuteczność ceramicznych materiałów kompozytowych w warunkach ekstremalnego szoku termicznego.
Właściwości korozyjne
Dane dotyczące zachowania korozyjnego CMC są skąpe, z wyjątkiem utleniania w temperaturach powyżej 1000 °C. O tych właściwościach decydują składniki, a mianowicie włókna i osnowa. Ogólnie materiały ceramiczne są bardzo odporne na korozję. Szerokie spektrum technik wytwarzania z różnymi dodatkami spiekania, mieszaninami, fazami szklistymi i porowatościami ma kluczowe znaczenie dla wyników badań korozyjnych. Mniej zanieczyszczeń i dokładna stechiometria prowadzą do mniejszej korozji. Struktury amorficzne i nieceramiczne chemikalia często stosowane jako środki wspomagające spiekanie są punktami początkowymi ataku korozyjnego.
- Glinka
Czysty tlenek glinu wykazuje doskonałą odporność na korozję w przypadku większości chemikaliów. Amorficzne fazy szkła i krzemionki na granicach ziaren determinują szybkość korozji w stężonych kwasach i zasadach oraz powodują pełzanie w wysokich temperaturach. Te cechy ograniczają użycie tlenku glinu. W przypadku stopionych metali tlenek glinu jest używany tylko ze złotem i platyną.
- Włókna z tlenku glinu
Włókna te wykazują właściwości korozyjne podobne do tlenku glinu, ale dostępne w handlu włókna nie są bardzo czyste i dlatego są mniej odporne. Ze względu na pełzanie w temperaturach powyżej 1000 °C istnieje tylko kilka zastosowań tlenkowych CMC.
- Węgiel
Najbardziej znacząca korozja węgla występuje w obecności tlenu powyżej około 500°C (932°F). Spala się, tworząc dwutlenek węgla i/lub tlenek węgla . Utlenia się również w silnych środkach utleniających, takich jak stężony kwas azotowy . W stopionych metalach rozpuszcza się i tworzy węgliki metali . Włókna węglowe nie różnią się od węgla zachowaniem korozyjnym.
- Węglik krzemu
Czysty węglik krzemu jest jednym z najbardziej odpornych na korozję materiałów. Tylko mocne zasady, tlen powyżej około 800°C (1470 °F) i stopione metale reagują z nim tworząc węgliki i krzemki . Reakcja z tlenem tworzy SiO
2i CO
2, przy czym warstwa powierzchniowa SiO
2spowalnia późniejsze utlenianie ( utlenianie pasywne ). Temperatury powyżej około 1600 ° C (2910 ° F) i niskie ciśnienie cząstkowe tlenu powodują tak zwane aktywne utlenianie , w którym CO, CO
2i powstają gazowe SiO powodujące szybką utratę SiC. Jeśli matryca SiC jest wytwarzana w inny sposób niż CVI, odporność na korozję nie jest tak dobra. Jest to konsekwencją porowatości w amorficznym LPI i resztkowego krzemu w matrycy LSI.
- Włókna z węglika krzemu
Włókna z węglika krzemu są wytwarzane przez pirolizę polimerów organicznych, a zatem ich właściwości korozyjne są podobne do właściwości węglika krzemu występującego w matrycach LPI. Włókna te są zatem bardziej wrażliwe na zasady i środki utleniające niż czysty węglik krzemu.
Aplikacje
Materiały CMC przezwyciężają główne wady konwencjonalnej ceramiki technicznej, a mianowicie kruche pękanie i niską odporność na pękanie oraz ograniczoną odporność na szok termiczny. Dlatego ich zastosowania znajdują się w dziedzinach wymagających niezawodności w wysokich temperaturach (poza możliwościami metali) oraz odporności na korozję i zużycie. Obejmują one:
- Systemy osłon termicznych dla pojazdów kosmicznych , które są potrzebne w fazie powrotu , gdzie występują wysokie temperatury, warunki szoku termicznego i duże obciążenia wibracyjne.
- Komponenty do wysokotemperaturowych turbin gazowych takie jak komory spalania , łopatki stojana , mieszacze spalin i łopatki turbin .
- Komponenty do palników , uchwytów płomienia i kanałów gorącego gazu, gdzie zastosowanie tlenkowych CMC znalazło zastosowanie.
- Tarcze hamulcowe i elementy układu hamulcowego, które doświadczają ekstremalnego szoku termicznego (większego niż wrzucenie żarzącej się części dowolnego materiału do wody).
- Komponenty do łożysk ślizgowych pod dużym obciążeniem, wymagające wysokiej odporności na korozję i zużycie.
Oprócz powyższego, CMC można stosować w zastosowaniach, w których stosuje się konwencjonalną ceramikę lub w których elementy metalowe mają ograniczoną żywotność z powodu korozji lub wysokich temperatur.
Opracowania do zastosowań w kosmosie
Podczas fazy powrotu pojazdów kosmicznych system osłony termicznej jest wystawiony na działanie temperatur powyżej 1500 °C (2730 °F) przez kilka minut. Tylko materiały ceramiczne mogą przetrwać takie warunki bez znaczących uszkodzeń, a spośród ceramiki tylko CMC są w stanie odpowiednio poradzić sobie ze wstrząsami termicznymi. Rozwój systemów osłony termicznej opartych na CMC zapewnia następujące korzyści:
- Zredukowana waga
- Większa nośność systemu
- Możliwość wielokrotnego użytku dla kilku ponownych wpisów
- Lepsze sterowanie w fazie powrotu z systemami klap CMC
W tych zastosowaniach wysokie temperatury wykluczają stosowanie CMC z włókien tlenkowych, ponieważ pod przewidywanymi obciążeniami pełzanie byłoby zbyt duże. Włókna amorficznego węglika krzemu tracą swoją wytrzymałość w wyniku rekrystalizacji w temperaturach powyżej 1250 °C (2280 °F). Dlatego w programach rozwojowych do tych zastosowań wykorzystuje się włókna węglowe w osnowie z węglika krzemu (C/SiC). Europejski program HERMES of ESA , rozpoczęty w latach 80-tych i zaniechany w 1992 roku z powodów finansowych, przyniósł pierwsze rezultaty. Kilka dalszych programów skupiło się na rozwoju, produkcji i kwalifikacji nakładki na nos, krawędzi natarcia i klap sterowniczych do pojazdu kosmicznego NASA X-38 .
Ten program rozwoju zakwalifikował użycie śrub i nakrętek C/SiC oraz systemu łożyskowego klap. Te ostatnie zostały przetestowane na ziemi w DLR w Stuttgarcie w Niemczech, w oczekiwanych warunkach fazy ponownego wejścia: 1600 ° C (2910 ° F), obciążenie 4 tony , ciśnienie parcjalne tlenu podobne do warunków ponownego wejścia i jednoczesne łożysko ruchy czterech cykli na sekundę. W sumie przeprowadzono symulację pięciu faz ponownego wejścia. Konstrukcja i produkcja dwóch klap kierowniczych oraz ich łożysk, śrub i nakrętek została wykonana przez MT Aerospace w Augsburgu w Niemczech w oparciu o proces CVI do produkcji węglika krzemu wzmocnionego włóknem węglowym (patrz procedury produkcyjne powyżej). Ponadto opracowano i zakwalifikowano systemy ochrony przed utlenianiem, aby zapobiegać wypalaniu się włókien węglowych. Po zamontowaniu klap, NASA z powodzeniem przeprowadziła testy mechaniczne naziemne w Houston w Teksasie. Kolejny test – prawdziwy powrót pojazdu bezzałogowego X-38 – został odwołany ze względów finansowych. Jeden z promów kosmicznych wprowadziłby pojazd na orbitę, skąd wróciłby na Ziemię.
Kwalifikacje te były obiecujące tylko dla tej aplikacji. Ładowanie wysokotemperaturowe trwa tylko około 20 minut na ponowne wejście, a do ponownego użycia wystarczyłoby tylko około 30 cykli. Jednak w zastosowaniach przemysłowych w środowisku gorących gazów wymagane jest kilkaset cykli obciążeń termicznych i nawet wiele tysięcy godzin żywotności.
The Intermediate eXperimental Vehicle (IXV), projekt zainicjowany przez ESA w 2009 roku, jest pierwszym w Europie pojazdem z podnoszonym nadwoziem do ponownego wjazdu. Opracowany przez Thales Alenia Space IXV ma odbyć pierwszy lot w 2014 roku podczas czwartej misji Vega (VV04) nad Zatoką Gwinejską. Do jego budowy przyczyniło się ponad 40 europejskich firm. System ochrony termicznej spodu pojazdu, składający się z nosa, krawędzi natarcia i dolnej powierzchni skrzydła, został zaprojektowany i wykonany przez firmę Herakles przy użyciu kompozytu z osnową ceramiczną (CMC), węgiel/węglik krzemu (C/SiC), w tym przypadku w oparciu o proces infiltracji ciekłym krzemem (LSI) (patrz procedury produkcyjne powyżej). Elementy te powinny były funkcjonować jako osłona cieplna pojazdu podczas jego powrotu do atmosfery.
Komisja Europejska sfinansowała projekt badawczy, C3HARME pod NMP-19-2015 wezwanie Programu Ramowego Badań i Rozwoju Technologicznego (H2020) w 2016 roku do projektowania, rozwoju, produkcji i testowania nowej klasy ultra-wysokiej kompozyty z osnową ceramiczną (UHTCMC) wzmocnione włóknami z węglika krzemu i włóknami węglowymi nadają się do zastosowań w trudnych warunkach lotniczych, takich jak układy napędowe i systemy ochrony termicznej (TPS).
Rozwój komponentów turbin gazowych
Zastosowanie CMC w turbinach gazowych pozwala na wyższe temperatury wlotu turbiny, co poprawia sprawność silnika. Ze względu na skomplikowany kształt łopatek stojana i łopatek turbiny, rozwój koncentrował się najpierw na komorze spalania. W USA komorę spalania wykonaną z SiC/SiC ze specjalnym włóknem SiC o zwiększonej stabilności w wysokich temperaturach z powodzeniem testowano przez 15 000 godzin. Utlenianie SiC zostało znacznie zmniejszone dzięki zastosowaniu powłoki ochronnej przed utlenianiem składającej się z kilku warstw tlenków.
Współpraca silników między General Electric i Rolls-Royce badała zastosowanie łopatek stojana CMC w gorącej części silnika turbowentylatorowego F136 , silnika, który nie pokonał Pratta i Whitneya F-135 do zastosowania w Joint Strike Fighter . Spółka joint venture CFM International używa CMC do produkcji wysokotemperaturowych osłon turbin. General Electric stosuje CMC w wyściółkach komory spalania, dyszach i osłonie turbiny odpornej na wysokie temperatury w swoim nadchodzącym silniku GE9X. Części CMC są również badane pod kątem zastosowań stacjonarnych zarówno w zimnych, jak i gorących sekcjach silników, ponieważ naprężenia wywierane na części wirujące wymagałyby dalszych prac rozwojowych. Ogólnie rzecz biorąc, trwa rozwój CMC do zastosowania w turbinach w celu zmniejszenia problemów technicznych i redukcji kosztów.
Po 1,5 miliarda USD inwestycji i 20 latach badań i rozwoju , do 2020 r. GE Aviation zamierza produkować rocznie do 20 t (44 000 funtów) prepregu CMC i 10 t włókna z węglika krzemu . Chemiczne osadzanie z fazy gazowej może nakładać powłoki na układaną taśmę włóknistą w dużych ilościach, a GE udało się infiltrować i odlewać części o bardzo wysokiej gęstości krzemu, przekraczającej 90% dla środowisk cyklicznego zmęczenia , dzięki obróbce termicznej.
Powłoki barierowe dla środowiska (EBC) do ochrony komponentów turbin gazowych
Powłoki chroniące środowisko (EBC) stanowią barierę dla CMC, zmniejszając ilość tlenu i innych substancji korozyjnych przed dyfuzją przez powierzchnię elementów CMC.
Wymagania projektowe dla EBC:
- Dopasowanie współczynnika względnego do składnika CMC w celu zmniejszenia prawdopodobieństwa pęknięcia
- Niska lotność w celu zminimalizowania korozji/recesji wywołanej stałymi działaniami
- Odporny na stopione połknięte cząstki
- Zdolność do wysokich temperatur
- Stabilność faz w wysokich temperaturach
- Kompatybilność chemiczna z CMC i dodatkowymi warstwami
- Wysoka twardość i wytrzymałość w celu ochrony przed uszkodzeniem przez ciała obce (FOD) i erozją
Zazwyczaj w przypadku powlekania za pomocą EBC wymagana jest warstwa wiążąca, aby zapewnić dobrą przyczepność do składnika CMC. NASA opracowała EBC oparty na zawiesinie, który zaczyna się od powłoki na bazie mulitu, a następnie jest nakładany dodatkowymi 2-3 warstwami. Aby EBC aktywnie chronił powierzchnię CMC, do warstwy zawiesiny należy dodać środki spiekające, aby utworzyć gęstą powłokę, która zablokuje przenikanie tlenu, gazowych i stopionych osadów z silnika. Spiekanie tworzy zagęszczoną powłokę i poprawia przyczepność i wydajność powłoki.
Obecnie prowadzone są badania mające na celu zwalczanie typowych przyczyn awarii, takich jak rozwarstwienie, erozja i pękanie spowodowane parą wodną lub stopionymi osadami. Delaminacja i pękanie z powodu stopionych osadów są zazwyczaj spowodowane reakcją z EBC tworzącą nieoczekiwaną mikrostrukturę prowadzącą do niedopasowania CTE i niskiej ciągliwości w tej fazie. Degradacja parowa jest spowodowana przez ulatnianie się termicznie rosnącej warstwy tlenkowej pomiędzy EBC a ceramiką. Wytworzona z tego para prowadzi do gwałtownej recesji SiC, tj. degradacji EBC. Sukces EBCs jest niezbędny dla ogólnego sukcesu komponentów CMC w przepływie gazu przez turbinę w silnikach odrzutowych.
Ogólne korzyści z EBC:
- Wydłuża żywotność komponentów CMC, pozwalając na ogólne oszczędności kosztów produkcji silników odrzutowych
- Poprawia odporność na utlenianie komponentów CMC
- Zapewnia większą odporność na utlenianie komponentów CMC narażonych na działanie związków gazowych z silnika odrzutowego
Zastosowanie tlenkowej CMC w palnikach i kanałach gorących gazów
Gaz zawierający tlen w temperaturach powyżej 1000 °C (1800 °F) jest raczej korozyjny dla elementów metalowych i z węglika krzemu. Takie elementy, które nie są narażone na duże obciążenia mechaniczne, mogą być wykonane z tlenkowych CMC, które wytrzymują temperatury do 1200 °C (2190 °F). Galerii poniżej przedstawia uchwyt płomienia z chrupkiego piekarni testowana po 15000 godzin, na który następnie działa przez w sumie więcej niż 20.000 godzin.
Uchwyt płomienia Oxide CMC | Wentylator gorących gazów | Brama podnoszona, oksydowana CMC | Brama podnoszona na polu |
Klapy i wentylatory przepuszczające gorące gazy zawierające tlen mogą być wykonane w tym samym kształcie, co ich metalowe odpowiedniki. Żywotność tych tlenkowych elementów CMC jest kilkakrotnie dłuższa niż w przypadku metali, które często się odkształcają. Kolejnym przykładem jest oksydowana brama podnosząca CMC do pieca do spiekania, która przetrwała ponad 260 000 cykli otwarcia.
Zastosowanie w tarczy hamulcowej
Węgiel / węgiel (C / C) materiały znalazły drogę do hamulców tarczowych z wyścigów samochodów i samolotów , a tarcze hamulcowe C / SiC produkowane przez proces LSI zakwalifikowano i są dostępne na rynku dla pojazdów luksusowych . Zaletami tych dysków C/SiC są:
- Producenci prognozują bardzo małe zużycie, skutkujące dożywotnią eksploatacją samochodu o normalnym obciążeniu wynoszącym 300 000 km (190000 mil).
- Brak blaknięcia , nawet przy dużym obciążeniu.
- Nie widać wpływu wilgotności powierzchni na współczynnik tarcia, jak w przypadku tarcz hamulcowych C/C.
- Odporność na korozję, na przykład na sól drogową, jest znacznie lepsza niż w przypadku krążków metalowych.
- Masa dysku to tylko 40% metalowego dysku. Przekłada się to na mniejszą masę nieresorowaną i wirującą.
Zmniejszenie masy poprawia reakcję amortyzatorów, komfort trzymania się drogi, zwinność, oszczędność paliwa, a tym samym komfort jazdy.
Matryca SiC LSI ma bardzo niską porowatość, co dość dobrze chroni włókna węglowe. Tarcze hamulcowe nie są narażone na temperatury powyżej 500 °C (932 °F) przez więcej niż kilka godzin w całym okresie eksploatacji. Utlenianie nie stanowi zatem problemu w tym zastosowaniu. O sukcesie tej aplikacji dla samochodów klasy średniej zadecyduje obniżenie kosztów produkcji.
Zastosowanie w łożyskach ślizgowych
Konwencjonalny SiC, lub czasami tańszy SiSiC , jest z powodzeniem stosowany od ponad 25 lat w łożyskach ślizgowych lub ślizgowych pomp . Pompowana ciecz sama w sobie dostarcza smaru do łożyska. Podstawą tego sukcesu jest bardzo dobra odporność korozyjna na praktycznie wszystkie rodzaje mediów oraz bardzo niskie zużycie i niskie współczynniki tarcia . Łożyska te składają się z łożyska statycznego, pasowanego skurczowo w metalowym otoczeniu oraz obracającej się tulei wału zamontowanej na wale. Pod naprężeniem ściskającym ceramiczne łożysko statyczne ma małe ryzyko uszkodzenia, ale tuleja wału SiC nie ma takiej sytuacji i dlatego musi mieć dużą grubość ścianki i/lub być specjalnie zaprojektowana. W dużych pompach z wałami o średnicy 100–350 mm (3,9–13,8 cala) ryzyko awarii jest wyższe ze względu na zmieniające się wymagania dotyczące wydajności pompy – na przykład zmiany obciążenia podczas pracy. Wprowadzenie SiC/SiC jako materiału tulei wału okazało się bardzo udane. Eksperymenty na stanowisku badawczym wykazały prawie trzykrotną nośność właściwą systemu łożyskowego z tuleją wału wykonaną z SiC/SiC, spiekanym SiC jako łożyskiem statycznym i wodą o temperaturze 80 °C (176 °F) jako smarem. Wydajność specyficzne obciążenie łożyska jest zwykle podawana w W / mm 2 i oblicza się jako iloczyn obciążenia (MPa), prędkość powierzchni łożyska (m / s) i współczynnik tarcia; jest równa utracie mocy układu łożyskowego z powodu tarcia.
Ta koncepcja łożyska ślizgowego, a mianowicie tulei wału SiC/SiC i łożyska SiC, jest stosowana od 1994 roku w aplikacjach takich jak pompy wody zasilającej kotły w elektrowniach , które pompują kilka tysięcy metrów sześciennych ciepłej wody na poziom 2000 m (6600 ft), w cylindrycznej obudowie pompy wodociągach i wodą morską do odsalania roślin pompowania do 40.000 m 3 (1.400.000 stóp sześciennych) na poziomie około 20 m (66 ft).
Ten system łożyskowy został przetestowany w pompach do ciekłego tlenu , na przykład w turbopompach tlenowych silników pędowych rakiet kosmicznych, z następującymi wynikami. SiC i SiC/SiC są kompatybilne z ciekłym tlenem. W teście samozapłonu zgodnie z francuską normą NF 28-763 nie zaobserwowano samozapłonu w przypadku sproszkowanego SiC/SiC w czystym tlenie 20 bar w temperaturach do 525°C (977°F). Testy wykazały, że współczynnik tarcia wynosi połowę, a zużycie jednej pięćdziesiątej standardowych metali stosowanych w tym środowisku. Hydrostatyczny układ łożyskowy (patrz rysunek) przetrwał kilka godzin przy prędkości do 10 000 obrotów na minutę, przy różnych obciążeniach i 50 cyklach stanów przejściowych start/stop bez znaczących śladów zużycia.
Inne aplikacje i rozwój
- Klapy kontroli ciągu do wojskowych silników odrzutowych
- Komponenty do reaktorów termojądrowych i rozszczepialnych
- Systemy cierne do różnych zastosowań
- Zastosowania jądrowe
- obróbka cieplna, wysoka temperatura, oprawy lutownicze
Bibliografia
Dalsza lektura
- Kriegesmann, J., wyd. (2005). DKG Technische Keramische Werkstoffe . Ellerau: HvB-Verlag. Numer ISBN 978-3-938595-00-8.
- Krenkel, W., wyd. (2008). Kompozyty z osnową ceramiczną . Weinheim: Wiley-VCH. Numer ISBN 978-3-527-31361-7.
- Bansal, NP, wyd. (2005). Podręcznik kompozytów ceramicznych . Boston: Kluwer. Numer ISBN 1-4020-8133-2.
- Bansal, NP i Lamon, J., wyd. (2015). Kompozyty z osnową ceramiczną: materiały, modelowanie i technologia . Hoboken: Wiley. Numer ISBN 978-1-118-23116-6.